Should I upgrade to Ceramic Bearings
As cyclists, we are always searching for the holy grail, that perfect ride delivered by the ultimate machine. To achieve perfection, we change our bikes and even make significant upgrades that offer marginal gains in performance. Maybe – we can finally get there if we go for a more aero frame, lighter components, or deeper wheels. In that ongoing quest for that perfect ride, we sometimes overlook a straightforward solution, upgrade from steel to ceramic bearings.
Ceramic bearings are not cheap, but it’s more affordable than a brand-new bike. So is the upgrade worth it? Things to consider performance and durability.
Bearings impact on performance
Let’s compare steel to ceramic bearings in terms of wattage*. If we were to set up a theoretical test trial, riding at 250 watts and having all the same conditions: identical bike, road surface, wind, tires, and tire pressure; we are likely to see an increase in the speed/performance on the ceramic bearings because the ceramic bearing offers less friction. Due to the exacting manufacturing process, ceramic bearings are rounder, have a smoother surface, and their sizes are more uniform. All these factors help reduce friction. Less friction means less expenditure of energy required to spin your wheels. Your bike will accelerate faster and hold speed more efficiently.
Durability
A critical factor in determining if ceramic bearings are a worthy upgrade is considering the durability of the bearing. Less friction is desirable, especially at the low cost of only a few hundred dollars, but how long do they last?
Hardness is one of the main influencers on the longevity of a ceramic bearing. A high-quality ceramic bearing is 30% harder than a steel bearing which translates into longer lasting.
Not all bearings are created equal.
As you weigh out your options for a ceramic bearing upgrade, it’s critical to remember that some factors in your bearing choice are as important as steel or ceramic considerations. The grease used and the seal that protects the bearing can have as much or more impact on performance than the ball bearing itself. Do your homework; not all ceramic bearings are created equal. As you consider this upgrade keep in mind many low-cost ceramic bearings out on the market can create more friction than a steel bearing. So the quality of the ceramic bearing matters.
Note for this article; we will be talking about hybrid sealed bearings.
The tech on ceramic bearings
The internal elements on both ceramic and standard Steel bearings are the same; what makes the difference is the
- Material used
- Manufacturing process
- Machining tolerance
How are steel ball bearings made?
As the name suggests, a steel bearing has inner and outer races and ball bearings, all made from steel. The separator, commonly made from hard plastic is the only component not made from steel.
Steel bearings are inexpensive, but when they start grinding down and it’s time to replace them, it’s cheaper to buy new ones than to repair your existing ones.
Typically steel ball bearings are sections of a cut metal rod punched into a sphere shape. It is put into a grinder removing a large percentage of any material left over from the punching process. They then use a series of machines that smooth and polish the balls, with the whole process taking two to three days from start to finish—such a quick turnaround.
How are Ceramic Ball Bearings made?
The ceramic bearings manufacturing process can take up to two months to produce. It’s a lengthy process with several steps involved. The first step in creating a ceramic bearing is forming the ball. The material used in creating a ceramic bearing is silicone nitrate powder and utilizes hot isostatic pressing. The powder is compressed into a ball and then exposed to heat and further compression for approximately 30 hours. The long exposure under heat and compression allows the material to condense further, helping to get the ceramic bearing closer to the final mandated size.
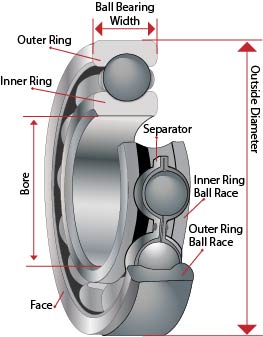
Cooling Process
After the ball is formed, add 30 hours more to cool and release the pressure; timing is critical. The bearings will become brittle or shatter if the correct timetable/protocol is not followed.
Lapping Process
The cooled bearings then go through the lapping process. “Lapping is used to describe several
various surface finishing operations where loose abrasive powders are used as the grinding
agent at normally low speeds. It is a process reserved for products that demand
very tight tolerances”. –Precision-surface.com
“The uniform radius and finish of the lapping ball are transferred to the bearing raceway. The irregularities in the raceway surface are substantially eliminated, thus retarding the onset of wear and greatly increasing bearing life.” –LapMaster.com
Polishing Process
The last part of the process is polishing with a slurry and water. The slurry polishes the bearings and removes any raised sections. The water polishing finishes the process resulting in a bearing surface that is ultra smooth with the sphericity measuring 0.001mm. The result is a ball that is 400% smoother, 128% stronger, and 58% lighter than a steel ball bearing.
The balls
A ceramic ball moves and spins more easily and distributes the load more evenly, being stronger(thus compressing less) and rounder and requiring less grease to run smoothly.
Grease
Less grease equates to less effort in overcoming friction, and friction slows you down.
You can run almost anything in a bearing to act as a lubricant. A thin chain lube in a brand new or well-cleaned bearing will be the fastest option, but it will have a life span of less than 100miles. The opposite would be marine waterproof grease which not even a jet wash seems able to dislodge but will roll significantly slower. Slic honey or a low-viscosity grease would be a great middle-ground for long service intervals and low friction. Ceramic bearings are priced higher because they come with higher-quality grease.
Seals
The seals dictate how much outside contamination can get into your bearings. If you run without seals, there will be very little friction; however, external contaminants, such as water, grit, or dirt, could enter the bearing. Water penetrating the bearing would corrode the steel; if grit and dirt penetrated the seal, they would deform the balls and the inner and outer race, causing premature wear and friction.
Why not run your bike with no seals in the bearing? It would be the faster option, but it’s a terrible idea unless you have a team of mechanics and parts at your disposal. Going in the opposite direction has its drawbacks too. You could have a very stiff seal completely impervious to the elements, which would be excellent for the life span of the bearing, but try spinning your wheel. It would stop almost instantly.
There is a middle ground that most companies have found. Some companies like Kogal offer options for different seals depending on the conditions and discipline. Road seals for those race day wheels in very dry climates and Cross seals for the wet winter months or for those who ride their ceramic wheels every day.
Ceramics can result in increased longevity and free speed.
What does all this mean in the real world, and what difference will it make to my ride? Longevity and free speed are ultimately what you are getting when you purchase a quality set of ceramic bearings.
Regarding your wheels, having smooth bearings can make a huge difference in ride quality. If you are looking for additional ways to go faster and further, then consider upgrading to ceramic bearings. We stand by our steel bearings as the industry standard, but we are delighted to provide a super high-quality Kogel ceramic bearing upgrade at a nominal $250 upcharge.
Happy riding!