The Heart of the Gulo Wheel System, the G-Spoke.
The heart of the Gulo Integrated wheel system is the G-Spoke
The Gulo Integrated Wheel System is unique to the Gulo brand due to the G-Spoke carbon spoke. Our spoke was developed utilizing the carbon composite manufacturing process called triaxial braiding in which Gulo’s parent company KEIR Manufacturing has deep experience in. KEIR has produced composite structures for the wire and cable and other industries for over 40 years.
What is the Triaxial Branding process?
Triaxial braiding, uses strands of raw fiber and are braided into 3-dimensional structures. This approach of braiding the fibers in any number of orientations gives the ability to control many variables in the finished product. It also allows the freedom to produce tiny parts, like a small, thin rod, such as the G-Spoke. After thousands of hours of research, development, and testing, the G1 Spoke was developed utilizing KEIR’s expertise in the carbon composite manufacturing process. The resulting spoke design was lightweight, impact-resistant, easy to build, and service into the Gulo Integrated Wheel System.
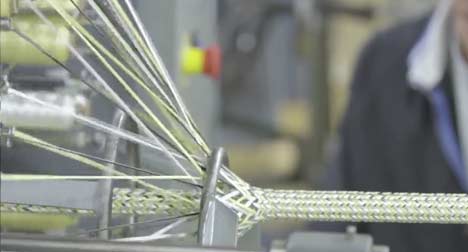
Modern-day bicycle wheels
Modern-day bicycle wheels are primarily the same as their predecessors. Although the components used (rims, hubs, spokes) have made advances, the wheel system has remained relatively unchanged. The bicycle wheel is a reasonably reliable system; however, many issues can occur and result in failures, given enough time and use.
Underlying problems associated with most bicycle wheels include:
• Spoke fatigue
• Rim fatigue
• Spoke elongation
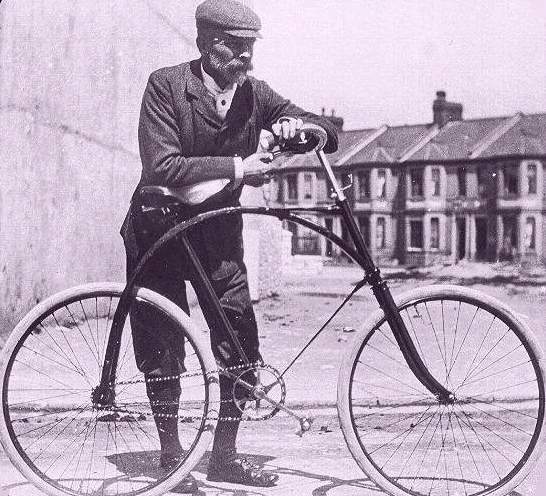
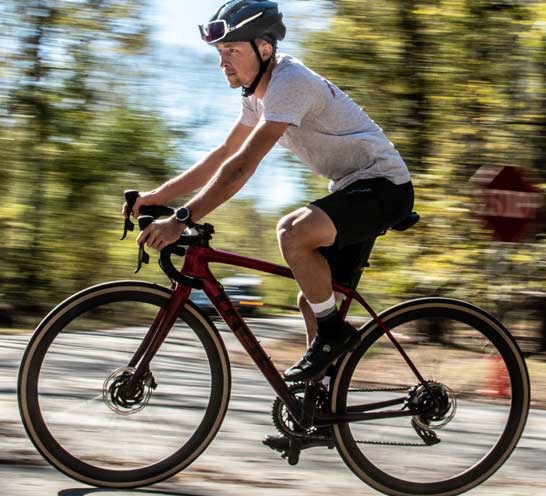
What is Spoke Fatigue
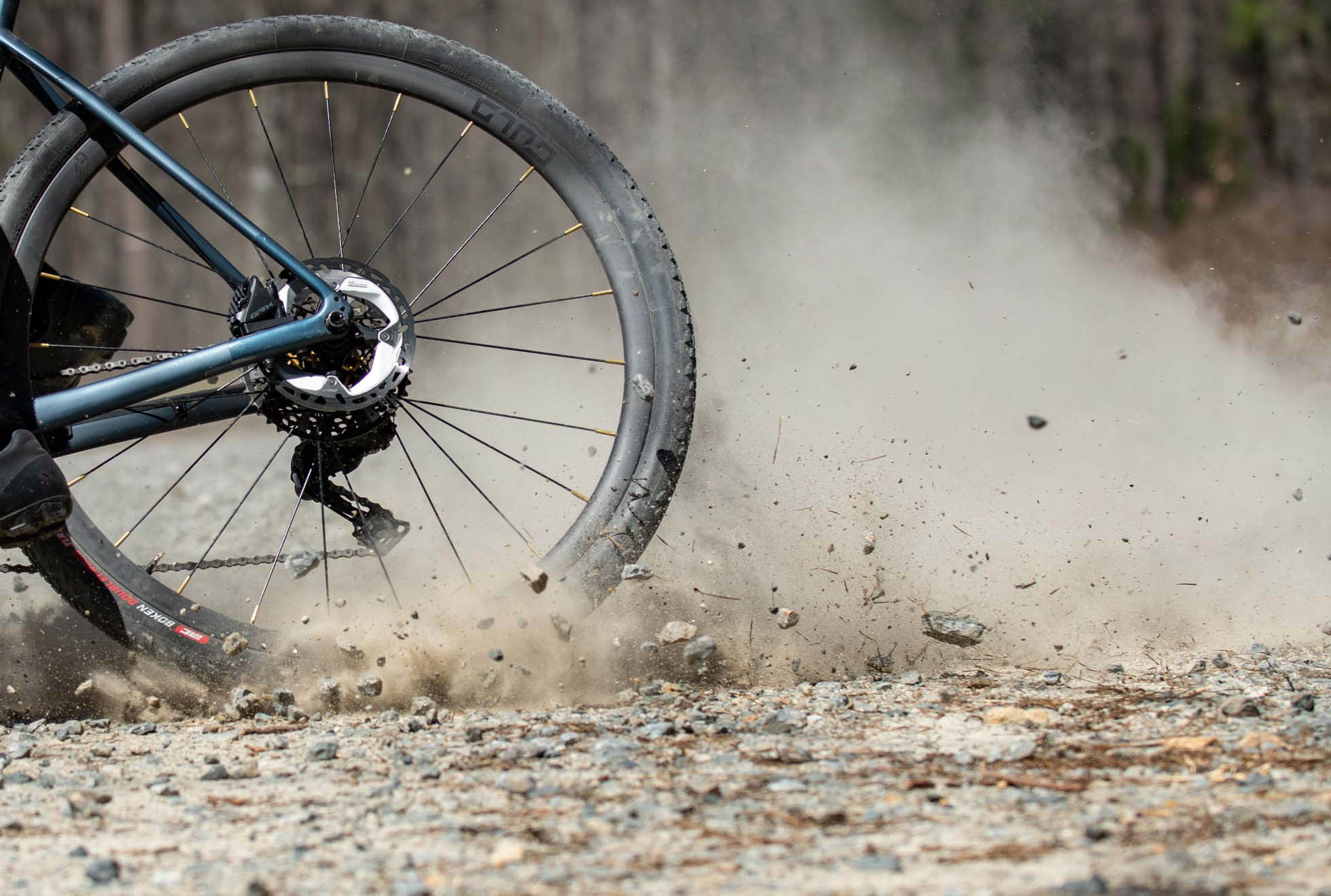
Spoke fatigue results from the loading/unloading cycles every spoke goes through during each wheel’s revolution. In most wheel systems today, the spokes (usually j-bend) are stressed and point loaded in at least 2, sometimes 3 locations along the spoke length.
• Hub flange: the spokes are bent to achieve a straighter path in crossing their partner spokes.
• Cross-point: where two spokes touch one another, they make another small bend. That bend is necessary so that the spoke can reach its target point at the rim.
• Rim hole: the spoke undergoes one final harsh bend, as it enters a rim hole that is drilled at an arbitrary angle and gets fastened with a nipple that usually sits upright at 90* angle to the rim bed.
Spokes forced into alignment cause localized stress points, most notably at the hub flange and rim bed. These localized stress points go through cyclic loading, which causes cracks to occur, which causes the spoke to break. Imagine a system that alleviated those stress points?
For a deep dive into Spoke Fatigue you can read Bicycle-Wheel Spoke Patterns and Spoke Fatigue, by
Henri P. Gavin, Asst. Prof., Dept of Civ. Eng., Duke Univ.
Rim Fatigue
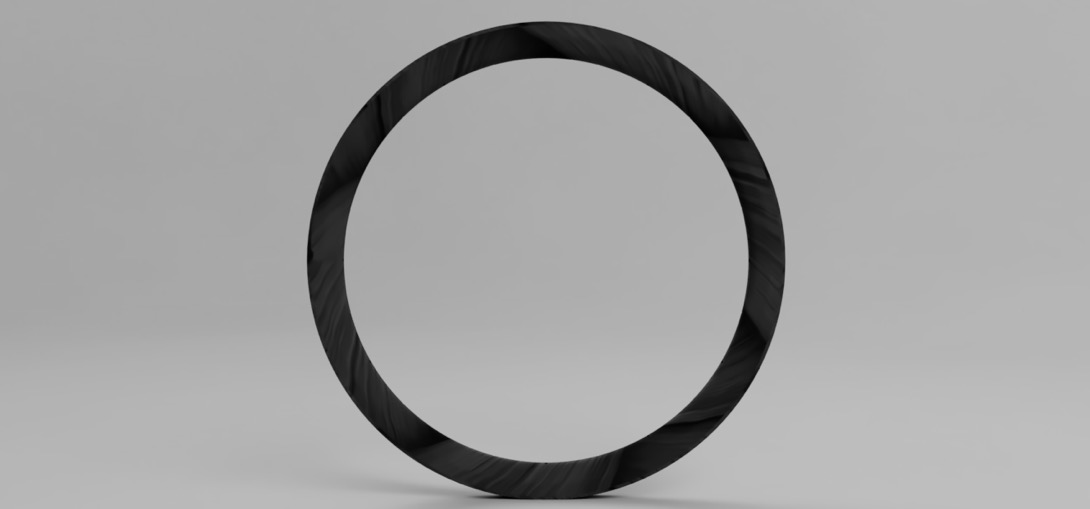
Much like spoke fatigue, the wheel rim undergoes thousands of load/unload cycles during each ride. Stress from loading/unloading is localized to the spoke holes as the spokes are trying to pull their way through the hole. In this scenario, two factors can either exacerbate or alleviate those stresses: geometry and material choice.
The geometry of those holes in the rim is critical. Holes drilled at a 90° angle to the rim, forcing the spoke into an unnatural bend. This bend means that the spoke will contact one side of the hole and impart a very high-stress load at that point
Bill Mould, a master wheel builder, said,
“In this scenario, you have a ticking time bomb; either the spoke or the rim will eventually develop fatigue cracks.”
In the Gulo Integrated System, the spoke holes are designed at very complex and necessary angles to alleviate any binding or side-loading at the spoke/rim interface. This complexity entails extremely dialed-in “side-to-side” angle and “fore-aft” angles; there are four unique hole drilling angles on each rim, each coinciding with where each spoke will land at the hub.
In material choice for Gulo rims, the solution is simple, carbon. Carbon has no discernible fatigue limit. Gulo wheel systems use carbon fiber rims manufactured to exacting specifications and quality levels to avoid the potential fatigue failures associated with aluminum rims. Aluminum has a relatively low endurance strength (related to fatigue limit) compared to other metals, which means that small localized stresses can cause fatigue cracking.
Gulo carbon rims help complete our high-end package into a super lightweight and stiff system.
Spoke Elongation
Steel spokes elongate elastically. This elasticity means they can stretch and bounce back to their original size, like a rubber band. But they have an elastic limit, like silly putty. Once they hit that limit (force), they will no longer bounce back. This force is called plastic elongation.
How do these factors affect bicycle wheels?
Most bicycle wheels today rely on butted spokes to help with ride quality and weight. Spoke manufacturers produce some sophisticated butting profiles (double-butted, triple-butted, bladed, etc.) for different uses.
• Cheaper MTB wheels built on an alloy rim, the wheel manufacturer will typically choose a straight gauge spoke to help aid in wheel stiffness.
• High-end road wheels built on a carbon fiber rim, the wheel manufacturer will most likely use a bladed or triple butted spoke to help aid in compliance and drop weight.
Both of these selections have their drawbacks.
For the MTB wheel using straight gauge spokes, the spokes are not very elastic. The cyclic stresses going into each spoke will find their way to those high-stress areas, at the rim and hub. Spoke breakage caused by fatigue lowers the quality (most OEM) MTB wheel.
For the high-end road wheel using triple butted spokes, the spokes are very elastic, and the elasticity helps alleviate stresses at the rim and hub. The drawback to this extreme elasticity is that road wheels can feel flexy when on the gas, especially under braking with modern-day disc brake-equipped road bikes.
Once these spokes reach their elastic limit, easily accomplished via a small stick or rock strike, they are damaged, de-tensioned, and otherwise useless in the wheel.
The Gulo composite G-Spoke
Gulo composite G-Spoke is much stiffer than any standard steel spokes on the market. For the mountain bike world, this stiffness helps aid in pedaling and braking efficiency. The combination of our G-Spokes and carbon fiber rims adds durability and overall stiffness to the Gulo wheel systems.
Our MTB wheels have lower spoke counts due to the extra spoke stiffness, which also helps complement our carbon rims’ ride quality. For the road biking world, our spokes’ added stiffness makes sure that our super lightweight road wheels will not be flexy; in fact, they are some of the stiffest on the market. Since the composite G-Spoke is already one of the world’s lightest, we do not need to reduce our spoke counts to save weight.

The Gulo Integrated Wheel System promise
If you’re a gravel rider
• Vibration dampening over rough gravel and dirt roads.
• Enhanced tracking on the loose terrain with extra stability.
• Shop Gravel
If you’re a mountain biker
• Drop almost a pound off your bike with one of our wheel systems.
• Add incredible stiffness, especially under hard braking, when you need it the most.
• The ride quality of our wheels is unmatched. You will notice the unexpected compliance, direct feedback, and muted feel on the trail.
• Shop Mountain
If you’re a roadie
• A super lightweight wheel system, weight saving on those long climbs.
• Stiffer ride if you’re on a disc-brake-equipped bike, you want all the stiffness you can get. For that, there is no match to the Gulo road systems.
• Shop Road Series
You want a better riding, better performing, and more reliable wheel system on your bike at the end of the day. That is what the Gulo wheels system will do for you.
The Gulo Integrated Wheel System is unique to the Gulo brand due to the G-Spoke carbon spoke. Our spoke was developed utilizing the carbon composite manufacturing process called triaxial braiding in which Gulo’s parent company KEIR Manufacturing has deep experience in. KEIR has produced composite structures for the wire and cable and other industries for over 40 years.
What is the Triaxial Branding process?
Triaxial braiding, uses strands of raw fiber and are braided into 3-dimensional structures. This approach of braiding the fibers in any number of orientations gives the ability to control many variables in the finished product. It also allows the freedom to produce tiny parts, like a small, thin rod, such as the G-Spoke. After thousands of hours of research, development, and testing, the G1 Spoke was developed utilizing KEIR’s expertise in the carbon composite manufacturing process. The resulting spoke design was lightweight, impact-resistant, easy to build, and service into the Gulo Integrated Wheel System.
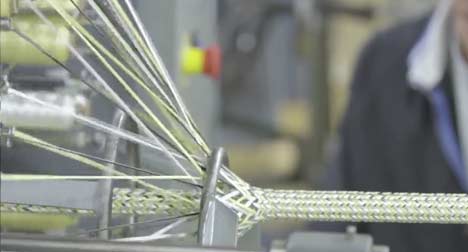
Modern-day bicycle wheels
Modern-day bicycle wheels are primarily the same as their predecessors. Although the components used (rims, hubs, spokes) have made advances, the wheel system has remained relatively unchanged. The bicycle wheel is a reasonably reliable system; however, many issues can occur and result in failures, given enough time and use.
Underlying problems associated with most bicycle wheels include:
• Spoke fatigue
• Rim fatigue
• Spoke elongation
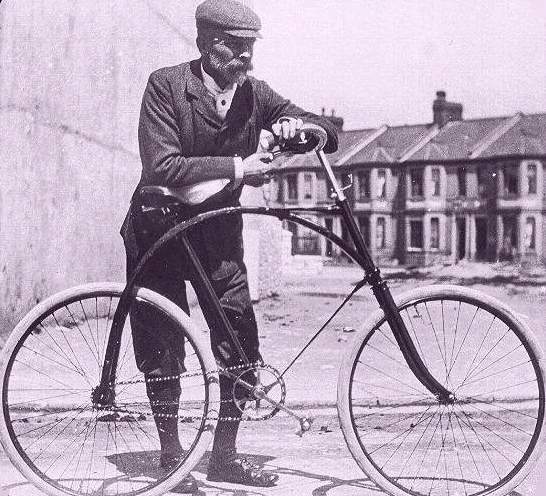
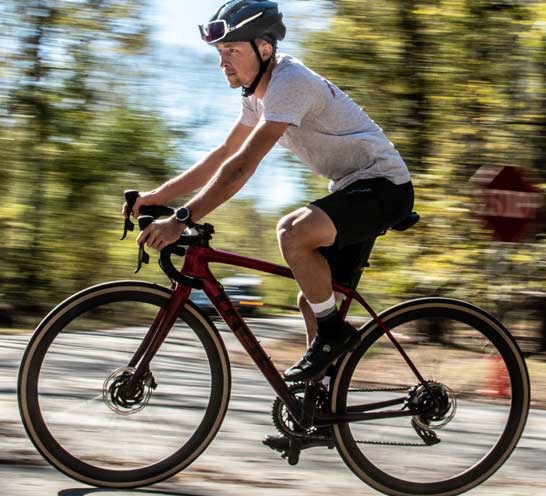
What is Spoke Fatigue
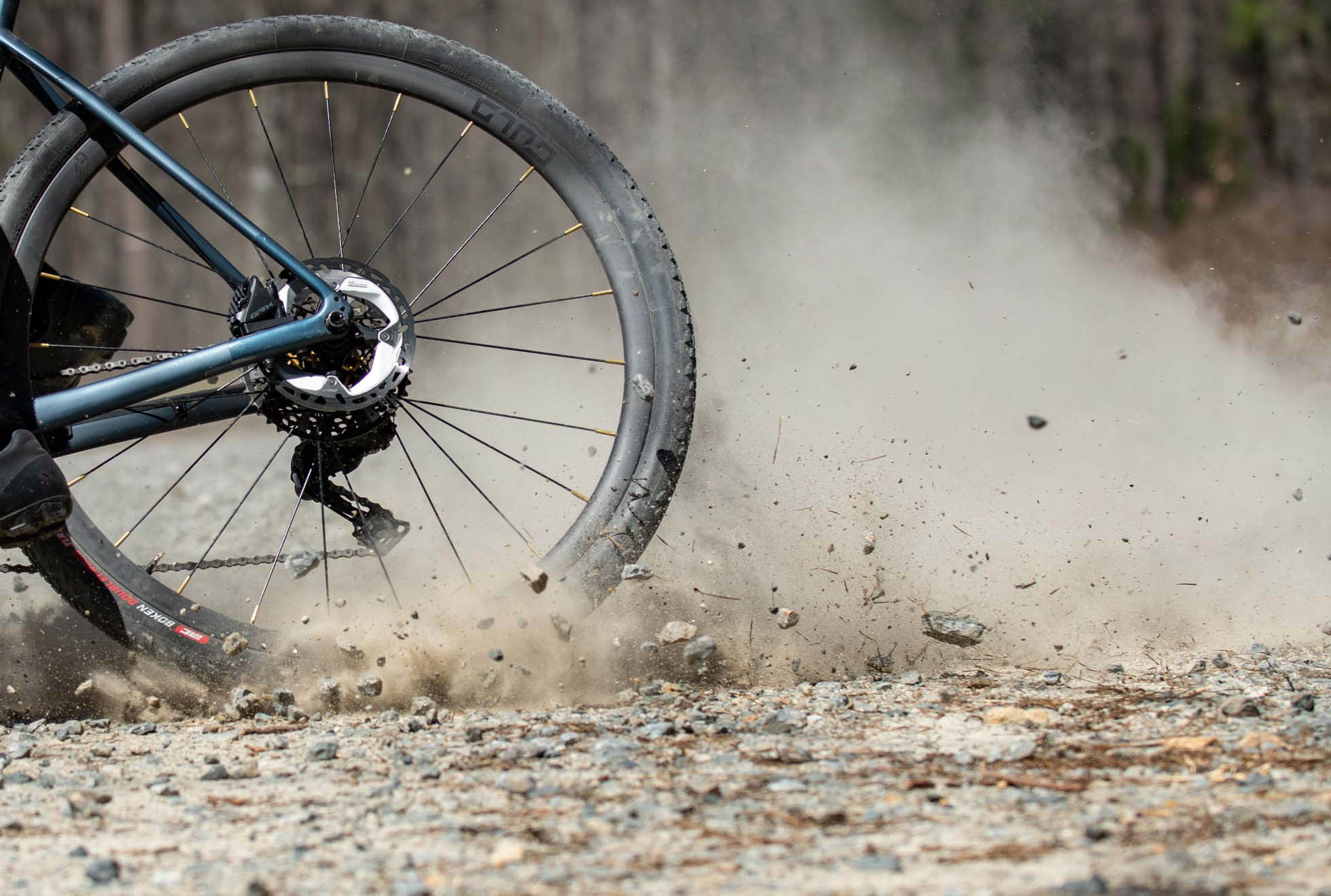
Spoke fatigue results from the loading/unloading cycles every spoke goes through during each wheel’s revolution. In most wheel systems today, the spokes (usually j-bend) are stressed and point loaded in at least 2, sometimes 3 locations along the spoke length.
• Hub flange: the spokes are bent to achieve a straighter path in crossing their partner spokes.
• Cross-point: where two spokes touch one another, they make another small bend. That bend is necessary so that the spoke can reach its target point at the rim.
• Rim hole: the spoke undergoes one final harsh bend, as it enters a rim hole that is drilled at an arbitrary angle and gets fastened with a nipple that usually sits upright at 90* angle to the rim bed.
Spokes forced into alignment cause localized stress points, most notably at the hub flange and rim bed. These localized stress points go through cyclic loading, which causes cracks to occur, which causes the spoke to break. Imagine a system that alleviated those stress points?
For a deep dive into Spoke Fatigue you can read Bicycle-Wheel Spoke Patterns and Spoke Fatigue, by
Henri P. Gavin, Asst. Prof., Dept of Civ. Eng., Duke Univ.
Rim Fatigue
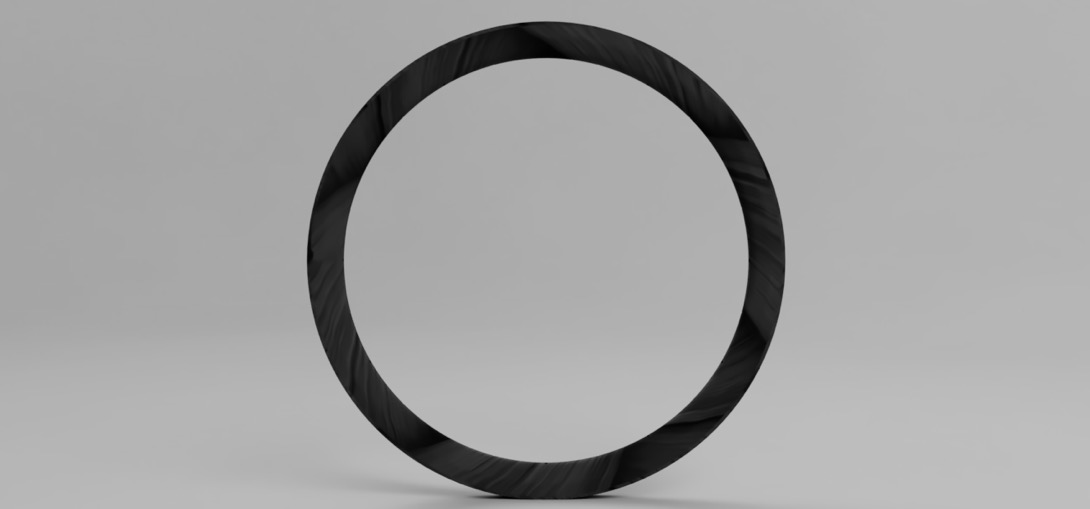
Much like spoke fatigue, the wheel rim undergoes thousands of load/unload cycles during each ride. Stress from loading/unloading is localized to the spoke holes as the spokes are trying to pull their way through the hole. In this scenario, two factors can either exacerbate or alleviate those stresses: geometry and material choice.
The geometry of those holes in the rim is critical. Holes drilled at a 90° angle to the rim, forcing the spoke into an unnatural bend. This bend means that the spoke will contact one side of the hole and impart a very high-stress load at that point
Bill Mould, a master wheel builder, said,
“In this scenario, you have a ticking time bomb; either the spoke or the rim will eventually develop fatigue cracks.”
In the Gulo Integrated System, the spoke holes are designed at very complex and necessary angles to alleviate any binding or side-loading at the spoke/rim interface. This complexity entails extremely dialed-in “side-to-side” angle and “fore-aft” angles; there are four unique hole drilling angles on each rim, each coinciding with where each spoke will land at the hub.
In material choice for Gulo rims, the solution is simple, carbon. Carbon has no discernible fatigue limit. Gulo wheel systems use carbon fiber rims manufactured to exacting specifications and quality levels to avoid the potential fatigue failures associated with aluminum rims. Aluminum has a relatively low endurance strength (related to fatigue limit) compared to other metals, which means that small localized stresses can cause fatigue cracking.
Gulo carbon rims help complete our high-end package into a super lightweight and stiff system.
Spoke Elongation
Steel spokes elongate elastically. This elasticity means they can stretch and bounce back to their original size, like a rubber band. But they have an elastic limit, like silly putty. Once they hit that limit (force), they will no longer bounce back. This force is called plastic elongation.
How do these factors affect bicycle wheels?
Most bicycle wheels today rely on butted spokes to help with ride quality and weight. Spoke manufacturers produce some sophisticated butting profiles (double-butted, triple-butted, bladed, etc.) for different uses.
• Cheaper MTB wheels built on an alloy rim, the wheel manufacturer will typically choose a straight gauge spoke to help aid in wheel stiffness.
• High-end road wheels built on a carbon fiber rim, the wheel manufacturer will most likely use a bladed or triple butted spoke to help aid in compliance and drop weight.
Both of these selections have their drawbacks.
For the MTB wheel using straight gauge spokes, the spokes are not very elastic. The cyclic stresses going into each spoke will find their way to those high-stress areas, at the rim and hub. Spoke breakage caused by fatigue lowers the quality (most OEM) MTB wheel.
For the high-end road wheel using triple butted spokes, the spokes are very elastic, and the elasticity helps alleviate stresses at the rim and hub. The drawback to this extreme elasticity is that road wheels can feel flexy when on the gas, especially under braking with modern-day disc brake-equipped road bikes.
Once these spokes reach their elastic limit, easily accomplished via a small stick or rock strike, they are damaged, de-tensioned, and otherwise useless in the wheel.
The Gulo composite G-Spoke
Gulo composite G-Spoke is much stiffer than any standard steel spokes on the market. For the mountain bike world, this stiffness helps aid in pedaling and braking efficiency. The combination of our G-Spokes and carbon fiber rims adds durability and overall stiffness to the Gulo wheel systems.
Our MTB wheels have lower spoke counts due to the extra spoke stiffness, which also helps complement our carbon rims’ ride quality. For the road biking world, our spokes’ added stiffness makes sure that our super lightweight road wheels will not be flexy; in fact, they are some of the stiffest on the market. Since the composite G-Spoke is already one of the world’s lightest, we do not need to reduce our spoke counts to save weight.

The Gulo Integrated Wheel System promise
If you’re a gravel rider
• Vibration dampening over rough gravel and dirt roads.
• Enhanced tracking on the loose terrain with extra stability.
• Shop Gravel
If you’re a mountain biker
• Drop almost a pound off your bike with one of our wheel systems.
• Add incredible stiffness, especially under hard braking, when you need it the most.
• The ride quality of our wheels is unmatched. You will notice the unexpected compliance, direct feedback, and muted feel on the trail.
• Shop Mountain
If you’re a roadie
• A super lightweight wheel system, weight saving on those long climbs.
• Stiffer ride if you’re on a disc-brake-equipped bike, you want all the stiffness you can get. For that, there is no match to the Gulo road systems.
• Shop Road Series
You want a better riding, better performing, and more reliable wheel system on your bike at the end of the day. That is what the Gulo wheels system will do for you.